Dos and don’ts of a sustainable EV supply chain
Electric vehicle (EV) sales continue to rise. To better serve our customers, we’ve been developing and refining best practices for handling EVs since they entered the market 5 years ago. With our Zeebrugge terminal servicing as a major hub for EV exports and imports into markets across Europe, we’ve gathered some do’s and don’ts when it comes to ensuring quality and consistency across the supply chain to help mitigate risks for our customers, and ensure a steady flow of vehicles. Here’s what you need to know.
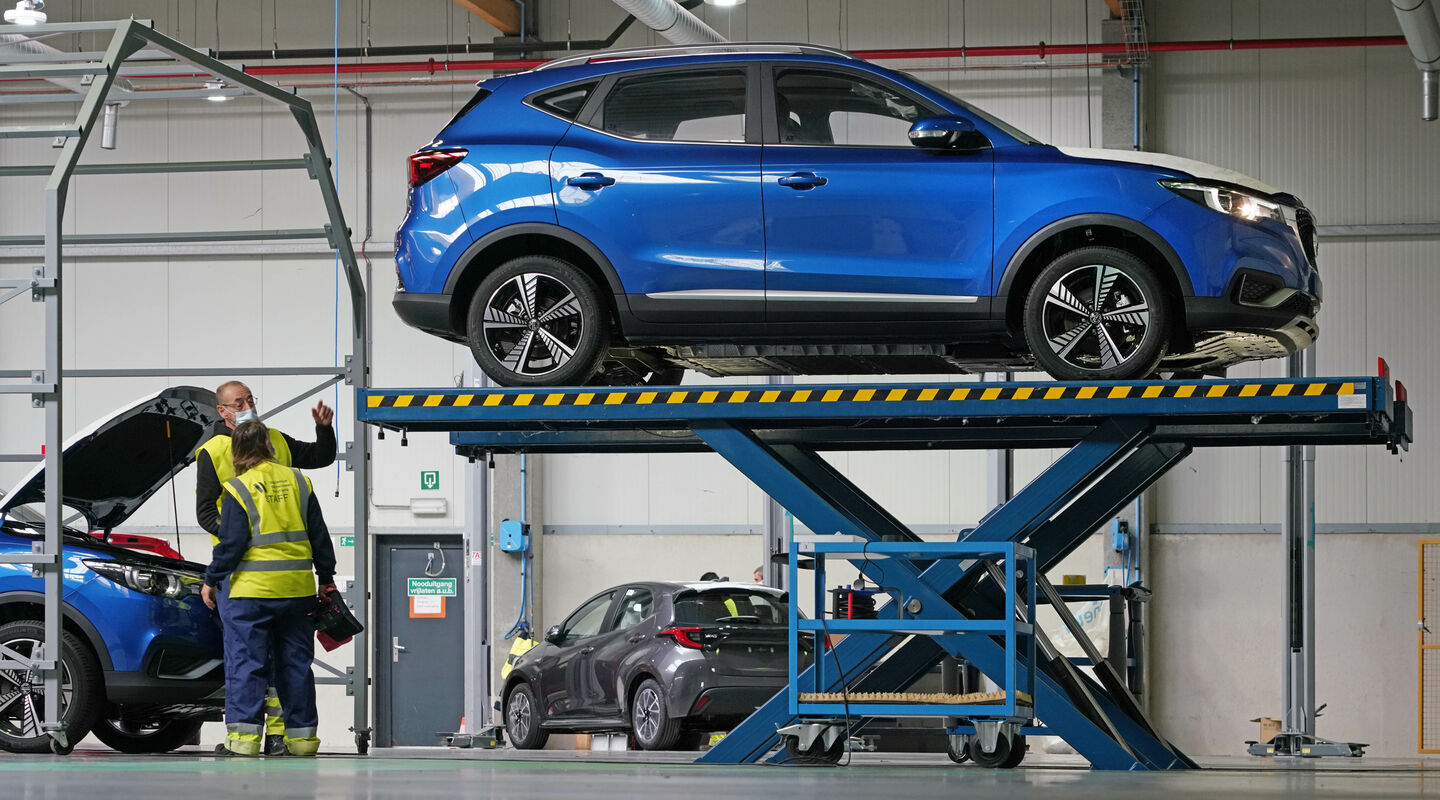
Risks to look out for
With our customers’ help, we’ve worked to identify root causes and create plans of action to correct any issues EVs might incur during their journey.
One of the most common issues is “non-starters” – where an EV has a dead battery and is unable to start.
Unlike traditional vehicles with internal combustion engines, EVs’ wheels lock when there is no power coming from the battery. This can interrupt operations, as special handling will be needed to move the vehicle.
So, whether a vehicle is unable to be unloaded from the vessel, shunted to a processing center, or into a staging area, on-site staff are trained to respond quickly to avoid any further delays throughout the entire operation.
“Together as a team, we’ve looked at how to address some of the key operations challenges linked to the electrification of the car industry,” says Daniel Woitzik – VPC manager, Zeebrugge. “Through our own experience and additional data we’ve been able to collect, we can be more proactive in addressing the root of disruptions to improve our operations and our customers’ speed to market.
It’s key that the terminal and the vehicle processing staff also work together to develop operational procedures to optimize cargo to reduce the risk of potential disruptions.
For example, some vehicles can be driven directly from the vessel to the processing center to avoid any extra vehicle moves that could deplete battery levels. If a vehicle cannot be started or moved, the team has a specially designed trolly on hand to transport the vehicle.
Safety, safety, safety (and proper training)
When choosing a partner to transport your vehicles, it’s important to know that safety and training are a priority for them.
With years of experience under their belt handling EVs, our Wallenius Wilhelmsen Zeebrugge teams have developed unique training to address issues safely. Our terminals have skilled technicians that can quickly address non-starters and other issues with EVs.
This means that operations do not need to be delayed for a long period waiting for third-party technicians to arrive and advise on what’s needed. All Wallenius Wilhelmsen technicians working on components of EVs in Zeebrugge accrue level 2 HEV certification. The rest of the staff received level 1 certification to highlight risks and safe ways of working with EVs.
With these certifications, the technicians can properly access batteries and other critical components of each model EV that comes through the facility. Whether that is to diagnose issues, learn how to jump-start vehicles, understand different types of chargers, lock and unlock certain areas of vehicles, and proper towing methods.
These procedures have been developed along with our customers and also aim to reduce the risks of working on batteries that contain potentially dangerous materials.
Through our on-port processing center, the Zeebrugge team has also developed maintenance programs to regularly check and inspect vehicles to ensure batteries and other crucial components of the vehicle are working properly. This includes monitoring battery levels to ensure they do not deplete while in storage. These steps ensure vehicles arrive at markets in ready condition and avoid any issues that may disrupt the rest of a vehicle’s journey.
“It is extremely gratifying to see these new processes go from initial planning to implantation in cooperation with our customers, who are all facing similar challenges. As the industry continues to prepare for the growing volumes of EVs, we are committed to maintaining quality while also ensuring our staff can continue to feel confident in the tasks that they are performing day in and day out,” adds Woitzik.